In other words, higher numbers translate to smaller openings in the screen the grains pass through. The ring test is designed to detect any cracks in a wheel.
Read: Grinding Wheel Safety: Respect The Maximum Speed.
3. When dulling begins, the abrasive fractures, creating new cutting points. The type of material affects the selection of abrasive, grit size and grade. While aluminum has been used in shipbuilding for decades, a growing number of other applications now use aluminum in metal fabrication due to its high strength-to-weight ratio and superior corrosion resistance. The goal when choosing a product for cutting, grinding and finishing aluminum is to have the right wheel or disc to address the needs of the pre-weld and post-weld operation. Another type of organic bond is rubber.
During grinding, the cutting points on the abrasive grains are worn flat; becoming increasingly blunt. Whatever kind of cutting job youre preparing for, set up for success by choosing the right type of grinding wheel. About the author: Joe Sullivan is senior product manager for Norton Company, Worcester, Massachusetts. Safety lessons from a welding equipment manufacturer, In The Workshop, Ep. It is not cost effective to grind aluminum, even skim passes, as it clogs the wheel so much and so fast that it does not "cut". Choosing the wrong product can cost the shop time and money. Another 472 in da house!
Many job shops start in a garage with a used mill and a manual lathe. Lets start by looking at the four most common abrasive materials: The Concrete Network recommends choosing a masonry wheel suited to the hardness of the concrete youre cutting. Non-woven discs and wheels are ideal for decorative finishing, satin and antique finishes, final sanding, soft metal finishing and fine burr removal. angle. The wheel itself comes in a variety of shapes. Grinding aluminum is best done with Coated abrasives. No representation is made that the information or references are complete or remain current.
The grinding wheel is one component in an engineered system consisting of wheel, machine tool, work material and operational factors. These pores are hollow spaces between abrasive grains and the bond , which help with the clearance of discarded metal chips in the grinding process. In most cases (particularly within maintenance, repair and operations) you would typically use a grinding wheel on an angle grinder. There are many different types of aluminum oxide abrasives, each specially made and blended for particular types of grinding jobs. grinding carbide dremel sharpening There are three principal types of bonds used in conventional grinding wheels. These wheels normally contain no wax or rubber fillers, which helps impede loading on hard-to grind They are well-suited to sharpening multi-tooth cutters and reamers, and for all precision grinding operations. Try our handy where to buy feature. The wheels are available in ceramic alumina, zirconia alumina, and aluminum oxide abrasives. Metalworkings leading information resource, Registration is Now Open for the 2022 Additive Manufacturing Conference at IMTS, Machining Questions? Wheels with vitrified bonds provide fast cutting. Folks, grinding aluminum is okay if you use the correct tools!
Resin fiber discs (RFDs) designated for aluminum are a good option for grinding, blending and finishing. What material will you be grinding and how hard is it? Grit refers to the size of the abrasive particles embedded in the wheela coarse 10 grit wheel uses abrasive particles that were sifted through a screen with ten holes per linear inch, whereas a 120 grit wheel uses finer abrasive particles that have been passed through a screen with 120 holes per inch. Before mounting a vitrified wheel, ring test it as explained in the American National Standards Institute's B7.1 Safety Code for the Use, Care and Protection of Grinding Wheels. Good question by the way. Because carbides, high speed steels, PCD, PCBN, ceramics and some other materials used to make cutting tools can be nearly as hard as conventional abrasives, the job of sharpening them falls to a special class of abrasives-diamond and the CBN, the superabrasives. (Courtesy of | Privacy Policy. They are suitable for imparting fine finishes, for small areas of contact, and for use with hard, brittle materials. Since 2005, the demand for the material has grown at a faster rate than any other metal or alloy primarily because of its increased popularity in additional market segments, such as structural framing, trailer manufacturing and repair, service decks and ladders, and platform construction. These bonds soften under the heat of grinding. There are 4 main types of abrasive grainsavailable for grinding wheels, these are: Often referred to as just Ceramic, Norton Quantums patented ceramic formof aluminium oxide isharder and sharper than conventional abrasive grains.
Use a matched pair of clean, recessed flanges at least one-third the diameter of the wheel. Never use a cracked wheel. Immediately after unpacking, all new wheels should be closely inspected to be sure they have not been damaged in transit. They also significantly reduce the noise and vibration through the cut, and are therefore easier to control. What grinding wheel grade should Ichoose? Easily access valuable industry resources now with full access to the digital edition of The FABRICATOR. There are nine main factors to be considered when selecting a grinding wheel for any application: 1. Thousands of these hard, tough grains move against the workpiece to cut away tiny chips of material. Abrasive suppliers offer a wide array of products for a wide array of grinding applications in metalworking. The result is an abrasive with the ability to fracture at a controlled rate at the sub-micron level, constantly creating thousands of new cutting points. This article is not a substitute for review of current applicable government regulations, industry standards, or other standards specific to your business and/or activities and should not be construed as legal advice or opinion. These are the basic ingredients of a thermite bomb, and there is a very real risk of a fire due to the reaction between the aluminum and the iron. Also, choose a finer grit when the project requires a closer, more precise operation over a smaller area of contact. The storage room should not be subjected to extreme variations in temperature and humidity because these can damage the bonds in some wheels. As a general guide, the harder the material, the softer the grade of wheel required. The best discs are pre-treated or coated with a lubricant to reduce heat buildup while grinding. Beeswax Ultimately, the right type of grinding wheel is going to offer a solid combination of cutting speed and durability at a price that makes sense for you. Never force grinding so that the motor slows noticeably or the work gets hot. Wheels with resinoid bonds are good choices for applications that require rapid stock removal, as well as those where better finishes are needed. Never attempt to alter the center hole.
These diamond metal bond wheels offer superior performance in round tool grinding. This question is safety oriented subject, which I feel is very important. On the other hand, wheels with the coarse grit and hard grade should be chosen for materials that are soft, ductile and easily penetrated. It's an abrasive cutting tool. The next factor to consider is the area of grinding contact between the wheel and the workpiece. Grit size is the size of individual abrasive grains in the wheel. The owners of this Utah job shop took a different tack. Applying pressure to increase performance will only lead to additional frustration and compromise quality. The product typically pictured when one thinks of a grinding wheel is the straight wheel. But unlike a saw, which has teeth only on its edge, the grinding wheel has abrasive grains distributed throughout the wheel. Aluminum powder or grinding swarf is potentially dangerous if it is mixed with iron or steel grinding wastes and is wet. Consult'g, Train'g& Software, About/Contact-Privacy Policy-1995-2022 finishing.com, Pine Beach, New Jersey, USA, (your purchases make finishing.com possible), Norton green silicon carbide grinding wheels, Saint-Gobain/ Norton Abrasives - McCordsville, Indiana. Check out our grinding.
The cutting wheel needs to be made of an abrasive suited to slicing through the stock youre working with and it needs to be bound with a material that can hold up to the stresses of the job. Lower numbers (such as 10, 16 or 24) denote a wheel with coarse grain.
Rubber bonds are often found in wheels used where a high quality of finish is required, such as ball bearing and roller bearing races. in Mechanical Engineering from the University of Tennessee, and has worked as a manufacturing engineer and tooling engineer in the steel and automotive industries for much of his career. After the wheel is securely mounted and the guards are in place, turn on the machine, step back out of the way and let it run for at least one minute at operating speed before starting to grind.
Also, a strong, consistent weld begins with proper surface preparation. Always make sure that all wheel and machine guards are in place, and that all covers are tightly closed before operating the machine. An ongoing discussion beginning back in 2004 Q. According to Grainger Metalworking Specialist, Mark Fine, selecting the right wheel will depend on the type of performance youre looking for. The expanding soft metal can apparently force the composite particles of the wheel apart in an explosive manner. Always use a wheel with a center hole size that fits snugly yet freely on the spindle without forcing it. Smaller areas of grinding contact require wheels with finer grits and harder grades to withstand the greater unit pressure. Going to a larger grit size and a very frangible resin will allow it to cut better, but you will go thru wheels very fast. This low melting temperature causes the material to coat the abrasive disc during grinding, covering the grit and exposing only bits of aluminum.
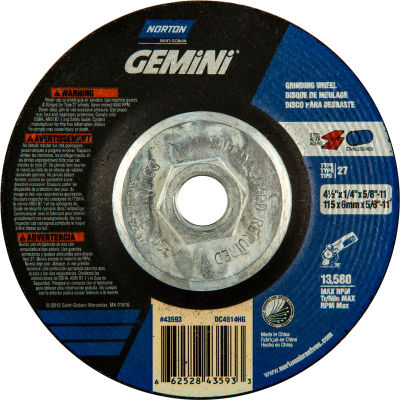
3. When dulling begins, the abrasive fractures, creating new cutting points. The type of material affects the selection of abrasive, grit size and grade. While aluminum has been used in shipbuilding for decades, a growing number of other applications now use aluminum in metal fabrication due to its high strength-to-weight ratio and superior corrosion resistance. The goal when choosing a product for cutting, grinding and finishing aluminum is to have the right wheel or disc to address the needs of the pre-weld and post-weld operation. Another type of organic bond is rubber.
During grinding, the cutting points on the abrasive grains are worn flat; becoming increasingly blunt. Whatever kind of cutting job youre preparing for, set up for success by choosing the right type of grinding wheel. About the author: Joe Sullivan is senior product manager for Norton Company, Worcester, Massachusetts. Safety lessons from a welding equipment manufacturer, In The Workshop, Ep. It is not cost effective to grind aluminum, even skim passes, as it clogs the wheel so much and so fast that it does not "cut". Choosing the wrong product can cost the shop time and money. Another 472 in da house!
Many job shops start in a garage with a used mill and a manual lathe. Lets start by looking at the four most common abrasive materials: The Concrete Network recommends choosing a masonry wheel suited to the hardness of the concrete youre cutting. Non-woven discs and wheels are ideal for decorative finishing, satin and antique finishes, final sanding, soft metal finishing and fine burr removal. angle. The wheel itself comes in a variety of shapes. Grinding aluminum is best done with Coated abrasives. No representation is made that the information or references are complete or remain current.
The grinding wheel is one component in an engineered system consisting of wheel, machine tool, work material and operational factors. These pores are hollow spaces between abrasive grains and the bond , which help with the clearance of discarded metal chips in the grinding process. In most cases (particularly within maintenance, repair and operations) you would typically use a grinding wheel on an angle grinder. There are many different types of aluminum oxide abrasives, each specially made and blended for particular types of grinding jobs. grinding carbide dremel sharpening There are three principal types of bonds used in conventional grinding wheels. These wheels normally contain no wax or rubber fillers, which helps impede loading on hard-to grind They are well-suited to sharpening multi-tooth cutters and reamers, and for all precision grinding operations. Try our handy where to buy feature. The wheels are available in ceramic alumina, zirconia alumina, and aluminum oxide abrasives. Metalworkings leading information resource, Registration is Now Open for the 2022 Additive Manufacturing Conference at IMTS, Machining Questions? Wheels with vitrified bonds provide fast cutting. Folks, grinding aluminum is okay if you use the correct tools!
Resin fiber discs (RFDs) designated for aluminum are a good option for grinding, blending and finishing. What material will you be grinding and how hard is it? Grit refers to the size of the abrasive particles embedded in the wheela coarse 10 grit wheel uses abrasive particles that were sifted through a screen with ten holes per linear inch, whereas a 120 grit wheel uses finer abrasive particles that have been passed through a screen with 120 holes per inch. Before mounting a vitrified wheel, ring test it as explained in the American National Standards Institute's B7.1 Safety Code for the Use, Care and Protection of Grinding Wheels. Good question by the way. Because carbides, high speed steels, PCD, PCBN, ceramics and some other materials used to make cutting tools can be nearly as hard as conventional abrasives, the job of sharpening them falls to a special class of abrasives-diamond and the CBN, the superabrasives. (Courtesy of | Privacy Policy. They are suitable for imparting fine finishes, for small areas of contact, and for use with hard, brittle materials. Since 2005, the demand for the material has grown at a faster rate than any other metal or alloy primarily because of its increased popularity in additional market segments, such as structural framing, trailer manufacturing and repair, service decks and ladders, and platform construction. These bonds soften under the heat of grinding. There are 4 main types of abrasive grainsavailable for grinding wheels, these are: Often referred to as just Ceramic, Norton Quantums patented ceramic formof aluminium oxide isharder and sharper than conventional abrasive grains.
Use a matched pair of clean, recessed flanges at least one-third the diameter of the wheel. Never use a cracked wheel. Immediately after unpacking, all new wheels should be closely inspected to be sure they have not been damaged in transit. They also significantly reduce the noise and vibration through the cut, and are therefore easier to control. What grinding wheel grade should Ichoose? Easily access valuable industry resources now with full access to the digital edition of The FABRICATOR. There are nine main factors to be considered when selecting a grinding wheel for any application: 1. Thousands of these hard, tough grains move against the workpiece to cut away tiny chips of material. Abrasive suppliers offer a wide array of products for a wide array of grinding applications in metalworking. The result is an abrasive with the ability to fracture at a controlled rate at the sub-micron level, constantly creating thousands of new cutting points. This article is not a substitute for review of current applicable government regulations, industry standards, or other standards specific to your business and/or activities and should not be construed as legal advice or opinion. These are the basic ingredients of a thermite bomb, and there is a very real risk of a fire due to the reaction between the aluminum and the iron. Also, choose a finer grit when the project requires a closer, more precise operation over a smaller area of contact. The storage room should not be subjected to extreme variations in temperature and humidity because these can damage the bonds in some wheels. As a general guide, the harder the material, the softer the grade of wheel required. The best discs are pre-treated or coated with a lubricant to reduce heat buildup while grinding. Beeswax Ultimately, the right type of grinding wheel is going to offer a solid combination of cutting speed and durability at a price that makes sense for you. Never force grinding so that the motor slows noticeably or the work gets hot. Wheels with resinoid bonds are good choices for applications that require rapid stock removal, as well as those where better finishes are needed. Never attempt to alter the center hole.
These diamond metal bond wheels offer superior performance in round tool grinding. This question is safety oriented subject, which I feel is very important. On the other hand, wheels with the coarse grit and hard grade should be chosen for materials that are soft, ductile and easily penetrated. It's an abrasive cutting tool. The next factor to consider is the area of grinding contact between the wheel and the workpiece. Grit size is the size of individual abrasive grains in the wheel. The owners of this Utah job shop took a different tack. Applying pressure to increase performance will only lead to additional frustration and compromise quality. The product typically pictured when one thinks of a grinding wheel is the straight wheel. But unlike a saw, which has teeth only on its edge, the grinding wheel has abrasive grains distributed throughout the wheel. Aluminum powder or grinding swarf is potentially dangerous if it is mixed with iron or steel grinding wastes and is wet. Consult'g, Train'g& Software, About/Contact-Privacy Policy-1995-2022 finishing.com, Pine Beach, New Jersey, USA, (your purchases make finishing.com possible), Norton green silicon carbide grinding wheels, Saint-Gobain/ Norton Abrasives - McCordsville, Indiana. Check out our grinding.
The cutting wheel needs to be made of an abrasive suited to slicing through the stock youre working with and it needs to be bound with a material that can hold up to the stresses of the job. Lower numbers (such as 10, 16 or 24) denote a wheel with coarse grain.
Rubber bonds are often found in wheels used where a high quality of finish is required, such as ball bearing and roller bearing races. in Mechanical Engineering from the University of Tennessee, and has worked as a manufacturing engineer and tooling engineer in the steel and automotive industries for much of his career. After the wheel is securely mounted and the guards are in place, turn on the machine, step back out of the way and let it run for at least one minute at operating speed before starting to grind.
Also, a strong, consistent weld begins with proper surface preparation. Always make sure that all wheel and machine guards are in place, and that all covers are tightly closed before operating the machine. An ongoing discussion beginning back in 2004 Q. According to Grainger Metalworking Specialist, Mark Fine, selecting the right wheel will depend on the type of performance youre looking for. The expanding soft metal can apparently force the composite particles of the wheel apart in an explosive manner. Always use a wheel with a center hole size that fits snugly yet freely on the spindle without forcing it. Smaller areas of grinding contact require wheels with finer grits and harder grades to withstand the greater unit pressure. Going to a larger grit size and a very frangible resin will allow it to cut better, but you will go thru wheels very fast. This low melting temperature causes the material to coat the abrasive disc during grinding, covering the grit and exposing only bits of aluminum.

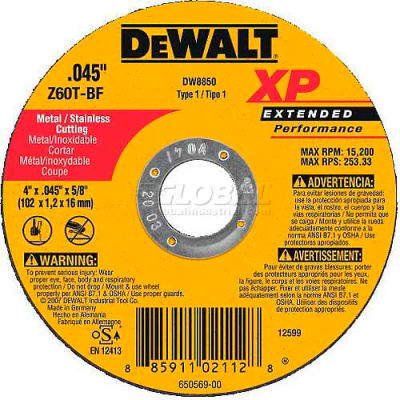
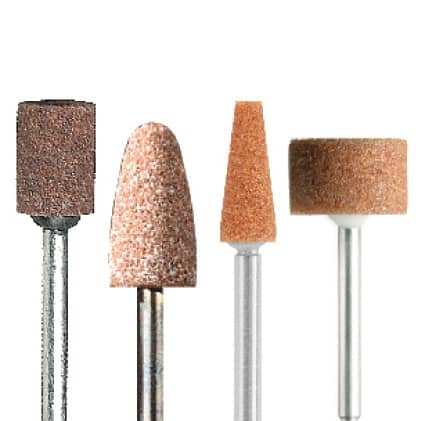