Well, since DLP is able to produce parts with such great dimensional accuracy, it's an ideal technology for the industry. Materials that are compatible with this printing technique include various photopolymerizable polymers, such as gelatin methacrylate (GelMA), poly(ethylene glycol) diacrylate (PEGDA), glycidyl methacrylate HA (GMHA), thiolated heparin (Hep-SH), and poly(glycerol sebacate) acrylate (PGSA) (Wang et al., 2019, 2020; Zhong et al., 2021). 9.18D shows that a shape memory Kelvin foam lattice structure and a printed chess structure can self-heal after the cut.
Bian et al. Using this method, a reversible shape-shifting structure with self-expanding/shrinking structures can be achieved (Fig. The limitation of DLP in comparison with SLA caused by voxels is the possible lack of details on a complex curved structure and the rougher curved surfaces. (A) Grayscale DLP printed multimaterials SMP for artificial arms with sequential shape recovery. However, there's always the good old general approximation. [165] utilized the graded stress by the nonuniform volume shrinkage during frontal photopolymerization to fold thin films into 3D origami structures. The way the laser cures the resin into layers is by "drawing" the layer's pattern on the bottom of the resin tank while curing the resin. Hi there! Naturally, everything starts with a 3D model. (8.9 and 8.10), respectively. All printed SMPs with different HDDA contents went through these four steps and the time spent of the fourth step was recorded to characterize the shape recovery rate. Shape Rf and shape Rr are two important parameters reflecting shape memory properties. (2009b) have utilized biodegradable PPF-based formulation to fabricate 3D scaffolds with a home-built DLP system. Image: Wevolver. 74.2E). Since DLP printers house a projector to project an image to be formed, they tend to be larger than other 3D printers. Besides printing SMP, DLP also enables digital manufacturing multimaterial for desolvation-based shape shifting [70,71,112,130,133,163,164]. Digital light processing (DLP) is another type of SLA. There are hundreds of different applications of DLP in the medical industry, but the most impressive one refers to the production of hearing aids. The jewelry industry is also one of those industries which require ultimate precision and great details, which makes a DLP 3D printer a perfect tool to help in the production. The subsequent swelling in a good solvent (such as acetone) drove the material to recovery. Kuang etal. Doctor of Philosophy from the University of Virginia in 1979, Dr. Howell has treated children, 1.16). By adding absorbers, for example in naphthol-based dye, the curing depth and the influence of scattered light can be adjusted, in order to achieve defined porosity and channels of bone scaffolds with a diameter of 300m. A team at the University of California, San Diego was able to 3D print nanoscopic fish-shaped objects, which help to perform toxin cleanup. What is the difference between DLP vs SLA? Under the same exposure time, with higher concentration of the polymers or the photoinitiators, the tissue construct becomes denser and stiffer. DLP printers are popular for their ability to quickly produce objects and parts with intricate designs with a high degree of accuracy. The test samples were processed into cylindrical shapes with the dimensions of 10mm2mm. The stiffness of these structures can be modified by increasing power from the light source or by modifying the duration of exposure which affects the degree of polymerization of the fabricated structure.
In December 2016, continuous DLP was transformed in a significant way by a Chattanooga, Tennessee-based startup named Collider. More specifically, the tBA is used for a monomer and HDDA serves as a crosslinker. In a recent publication by Heller et al. Sophie Laurenson. Therefore, the prepared photosensitive resins were very suitable for UV curing. DLP-based bioprinting systems incorporate light sources, digital micromirror device (DMD) chips, motorized stages, a holder for bioinks, an optional motorized printing head, and a computer control system that coordinates all components (Figure 2.1C) (Gou et al., 2014; Hribar, Soman, Warner, Chung, & Chen, 2014). His lectures on stress reduction, For example, the users define the print speed, layer height and support material positioning in the slicer. Moreover, the flexibility to fabricate complex 3D designs and integrate a variety of functional elements including live cells, biomaterials, and nanoparticles can be achieved with these computer-aided, photo-curing-based techniques [39].
It is limited to photopolymers that often emit odors that can be problematic in an office environment. A desk top Moonray DLP printer (Soonsolid, China) was used to make the photosensitive resin cured under a projection UV light. That process is repeated until the entire part is finished. Leave a comment if you think new innovations need to be added to this article! By moving the stage or the light focal plane along the z-direction, complex patterns can be fabricated in 3D. A native of Mobile, Alabama, Dr. Howell has lived and worked in Anniston since 1979. of personality typing and dynamics, which he has studied and taught for twenty years. Taking the preparation process of 10wt.% HDDA as an example, 10g HDDA was first slowly poured into 90g tBA to get a mixed solution, followed by the addition of 1g TPO and mixture for 3min with ultrasonic vibration, and then the homogeneous, sediment free and transparent liquid with low viscosity was obtained. A lively and energetic speaker, Dr. Howell is a regionally known workshop and seminar presenter. After that, the slicer quite literally virtually slices the 3D model into hundreds of layers. Similar to the inkjet-based 3D printing, LIFT also forms tissue constructs by depositing droplets (Fig. Inkjet-based 3D printers are designed based on the traditional 2D inkjet paper printer (Fig. In order to print prevascularized tissue constructs, the EC and GFs can be homogeneously mixed in the prepolymer solution to form the structure by SLA. Sophie Laurenson. The use of DLP technology enables curing of a whole layer at a time, thus eliminating the influence of path-planning procedures. When printing cells, no shear forces are applied, resulting in higher cell viability than inkjet- or extrusion-based bioprinters. As shown in Fig. Sang Jin Lee, in Principles of Tissue Engineering (Fifth Edition), 2020. Poly(ethylene glycol) (PEG) diacrylate (PEGDA), GelMA, Pluronic F127 DA, and hyaluronic acid (HA) MA are reported as potential biomaterials for DLP printing [40,41]. This ensures that the parts never stick to the build plate, excluding the need for the elevator to stop, but instead making it possible for the elevator to constantly move upwards. Fig. Origin has partnered with large chemical companies such as BASF, Henkel, and DSM to create unique photo polymers at a low cost that can be used to mass manufacture products. Up until recently the resins for DLP didn't exist in many colors (usually neutral color like black, white and grey), but new developments make that resins can have CMYK colored pigments added to them commercially, thus matching the wide range of colors you can get FDM filaments in. Min Tang, Shaochen Chen, in 3D Bioprinting and Nanotechnology in Tissue Engineering and Regenerative Medicine (Second Edition), 2022. Recently, Zhang etal. 9.19A, using the method of two-side illumination by two different grayscale patterns followed by releasing the mold, the cured sheet folded into origami Crane. The layer thickness was set to be 50m and the exposure time for each layer was set as 30s. The thermal stability and crystallization behavior of the DLP-fabricated specimens were analyzed by a TG/DSC synchronous thermal analyzer (STA449F3, Netzsch, Germany). Wevolvers free newsletter delivers the highlights of our award winning articles weekly to your inbox.
The light source (UV or visible) is reflected at the DMD chip, which contains 14 million micromirrors that can be rotated to be on or off using a simple binary mask. As mentioned, the printing material should be biodegradable and biocompatible so that living cells can be directly involved inside the droplets during the printing process. We use cookies to help provide and enhance our service and tailor content and ads. Most of the time, resins have a shelf life of about 1 year. In general, you're looking at around $350 and upwards per liter of such resin.As you can tell by the prices, the resin is quite more expensive than filament used for FDM 3D printing. 9.18C, an octet-truss microlattice in its original and deformed shape can load the same mass, which can further recover its unique shape upon heating up. Ali Davoudinejad, in Additive Manufacturing, 2021. Apart from that, Carbon's 3D printers are also special for creating a tiny zone of uncured resin which constantly flows between the part and the bottom of the vat.
So, the layers of a part printed on a DLP 3D printer are made of many 3D pixels called voxels. The resins for DLP are composed of tBA, HDDA, and TPO. He is married to Lark Dill Howell and they are the parents of Benton and Lauren. Studies have also shown that 3D printers reduced the returns of hearing aids caused by bad fittings. DLP cures an entire layer at once; SLA printers trace out a path with the laser, curing along that path. Another new additive manufacturing company is Origin, which focuses on creating a 3D printer that can be developed upon by material companies. 6.18b). 3D Systems Figure 4 augments continuous DLP with the use of industrial robotic arms. Dr. Howell also received in 1974, a Master of Arts in Religion from Yale Divinity School, where he Finally, the 3D scaffolds were successfully produced by DLP of unfilled (see Fig. After the slicing is done, We are left with a PNG stack of images that is flipped through like a picture book, one layer at a time until you reach the last layer of the model, our default layer thickness is 100um. The printing must be performed under sterile conditions when the cell-laden hydrogels are printed, and the printing materials should be mostly water-based and biocompatible. Due to it curing the entire layer at once, its much faster than SLA. (C) 3D cartoon face mask viewed from two different angles right after photopolymerization and the corresponding free bending of spatial, differently cured sheet. Well, parts printed DLP can be surprisingly strong considering the material they're made of - photopolymer resin - plastic. Fig. The major difference of DLP from laser-based SLA is that DLP uses a projection of ultraviolet (UV) light (or visible light) from a digital projector to flash a single image of the layer across the entire resin at once.
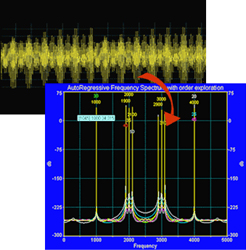
In December 2016, continuous DLP was transformed in a significant way by a Chattanooga, Tennessee-based startup named Collider. More specifically, the tBA is used for a monomer and HDDA serves as a crosslinker. In a recent publication by Heller et al. Sophie Laurenson. Therefore, the prepared photosensitive resins were very suitable for UV curing. DLP-based bioprinting systems incorporate light sources, digital micromirror device (DMD) chips, motorized stages, a holder for bioinks, an optional motorized printing head, and a computer control system that coordinates all components (Figure 2.1C) (Gou et al., 2014; Hribar, Soman, Warner, Chung, & Chen, 2014). His lectures on stress reduction, For example, the users define the print speed, layer height and support material positioning in the slicer. Moreover, the flexibility to fabricate complex 3D designs and integrate a variety of functional elements including live cells, biomaterials, and nanoparticles can be achieved with these computer-aided, photo-curing-based techniques [39].
It is limited to photopolymers that often emit odors that can be problematic in an office environment. A desk top Moonray DLP printer (Soonsolid, China) was used to make the photosensitive resin cured under a projection UV light. That process is repeated until the entire part is finished. Leave a comment if you think new innovations need to be added to this article! By moving the stage or the light focal plane along the z-direction, complex patterns can be fabricated in 3D. A native of Mobile, Alabama, Dr. Howell has lived and worked in Anniston since 1979. of personality typing and dynamics, which he has studied and taught for twenty years. Taking the preparation process of 10wt.% HDDA as an example, 10g HDDA was first slowly poured into 90g tBA to get a mixed solution, followed by the addition of 1g TPO and mixture for 3min with ultrasonic vibration, and then the homogeneous, sediment free and transparent liquid with low viscosity was obtained. A lively and energetic speaker, Dr. Howell is a regionally known workshop and seminar presenter. After that, the slicer quite literally virtually slices the 3D model into hundreds of layers. Similar to the inkjet-based 3D printing, LIFT also forms tissue constructs by depositing droplets (Fig. Inkjet-based 3D printers are designed based on the traditional 2D inkjet paper printer (Fig. In order to print prevascularized tissue constructs, the EC and GFs can be homogeneously mixed in the prepolymer solution to form the structure by SLA. Sophie Laurenson. The use of DLP technology enables curing of a whole layer at a time, thus eliminating the influence of path-planning procedures. When printing cells, no shear forces are applied, resulting in higher cell viability than inkjet- or extrusion-based bioprinters. As shown in Fig. Sang Jin Lee, in Principles of Tissue Engineering (Fifth Edition), 2020. Poly(ethylene glycol) (PEG) diacrylate (PEGDA), GelMA, Pluronic F127 DA, and hyaluronic acid (HA) MA are reported as potential biomaterials for DLP printing [40,41]. This ensures that the parts never stick to the build plate, excluding the need for the elevator to stop, but instead making it possible for the elevator to constantly move upwards. Fig. Origin has partnered with large chemical companies such as BASF, Henkel, and DSM to create unique photo polymers at a low cost that can be used to mass manufacture products. Up until recently the resins for DLP didn't exist in many colors (usually neutral color like black, white and grey), but new developments make that resins can have CMYK colored pigments added to them commercially, thus matching the wide range of colors you can get FDM filaments in. Min Tang, Shaochen Chen, in 3D Bioprinting and Nanotechnology in Tissue Engineering and Regenerative Medicine (Second Edition), 2022. Recently, Zhang etal. 9.19A, using the method of two-side illumination by two different grayscale patterns followed by releasing the mold, the cured sheet folded into origami Crane. The layer thickness was set to be 50m and the exposure time for each layer was set as 30s. The thermal stability and crystallization behavior of the DLP-fabricated specimens were analyzed by a TG/DSC synchronous thermal analyzer (STA449F3, Netzsch, Germany). Wevolvers free newsletter delivers the highlights of our award winning articles weekly to your inbox.
The light source (UV or visible) is reflected at the DMD chip, which contains 14 million micromirrors that can be rotated to be on or off using a simple binary mask. As mentioned, the printing material should be biodegradable and biocompatible so that living cells can be directly involved inside the droplets during the printing process. We use cookies to help provide and enhance our service and tailor content and ads. Most of the time, resins have a shelf life of about 1 year. In general, you're looking at around $350 and upwards per liter of such resin.As you can tell by the prices, the resin is quite more expensive than filament used for FDM 3D printing. 9.18C, an octet-truss microlattice in its original and deformed shape can load the same mass, which can further recover its unique shape upon heating up. Ali Davoudinejad, in Additive Manufacturing, 2021. Apart from that, Carbon's 3D printers are also special for creating a tiny zone of uncured resin which constantly flows between the part and the bottom of the vat.
So, the layers of a part printed on a DLP 3D printer are made of many 3D pixels called voxels. The resins for DLP are composed of tBA, HDDA, and TPO. He is married to Lark Dill Howell and they are the parents of Benton and Lauren. Studies have also shown that 3D printers reduced the returns of hearing aids caused by bad fittings. DLP cures an entire layer at once; SLA printers trace out a path with the laser, curing along that path. Another new additive manufacturing company is Origin, which focuses on creating a 3D printer that can be developed upon by material companies. 6.18b). 3D Systems Figure 4 augments continuous DLP with the use of industrial robotic arms. Dr. Howell also received in 1974, a Master of Arts in Religion from Yale Divinity School, where he Finally, the 3D scaffolds were successfully produced by DLP of unfilled (see Fig. After the slicing is done, We are left with a PNG stack of images that is flipped through like a picture book, one layer at a time until you reach the last layer of the model, our default layer thickness is 100um. The printing must be performed under sterile conditions when the cell-laden hydrogels are printed, and the printing materials should be mostly water-based and biocompatible. Due to it curing the entire layer at once, its much faster than SLA. (C) 3D cartoon face mask viewed from two different angles right after photopolymerization and the corresponding free bending of spatial, differently cured sheet. Well, parts printed DLP can be surprisingly strong considering the material they're made of - photopolymer resin - plastic. Fig. The major difference of DLP from laser-based SLA is that DLP uses a projection of ultraviolet (UV) light (or visible light) from a digital projector to flash a single image of the layer across the entire resin at once.