As with most competing technologies, both conventional and robotic palletizers have pros and cons. These can happen either manually or automatically, depending on the needs of the system. A pedestal-style robot mounted on a track can move between a series of pallets in a staging area. Commonly, a variety of conveyors will connect these pieces of equipment and network them to work in unison. safety safeguarding robotic palletizer packaging robotics cell applications robots functions operators communicating involved several device including status there packagingstrategies Their operation is relatively straightforward. Thanks to their advanced and robust design, they have extremely long maintenance intervals with an availability of 99.995 percent and maximum energy efficiency. Are there infeed conveyor systems in place that will need to be adapted, or will new conveyors need to be added? The palletizer of the KR QUANTEC PA family meets all of todays automation requirements:minimized space requirements, shorter cycles, maximum availability and low operating costs. You are using Internet Explorer and will not be able to use our website properly.Please change to an up-to-date browser for ideal presentation of the website.
This means that you know exactly how long it will take to form enough layers to fill a single pallet or a trailer load of pallets. Pallets need to be delivered, either manually or by a pallet dispenser. The simplicity of the design makes them also a very affordable option.
RobotWorx has helped hundreds of companies design the perfect palletizing system for their facility and application by incorporating a new or used palletizer.
palletizing robot intelligent
One customer came to them with a problem. Bag grippers encompass an item and support it on the bottom, while suction and magnetic grippers typically handle more ridged items and grip them from the top. Which in turn will improve morale and increase employee retention. 8720 Red Oak Blvd., Suite 201|Charlotte, NC 28217
The picking sequence is specified by the customers order lines and the valid stacking rules; Thus the source pallets have to be supplied in the pre-defined order.
source: IFA. robot palletizer palletizing palletizers systems goldpack packaging
However, the series of conveyors needed to orient the product means they also usually require more space. Sensors detect the current height of the top layer and the existence of slip sheets. These sensors allow for cooperation between humans and robots without any physical separation.
palletizer robot neetwk mecnicas tcnicas sold The layer picking robot can pull the whole layer with an integrated puller onto the gripper.
We've built a palletizing solution with the end useryouin mind. robot palletizer pick place industrial palletizing arm pallet gripper axis automatic application electric cost low motion handling upside 300mm installation And you can unsubscribe at any time. We offer our customers a full range of products and services from a single source. robotic palletizers bratney palletizer palletizing systems
), Presence of a linear axis, which most of the time cannot be power/force limited. Enter your industry and application and we will guide you to the right product or help you find matching case studies and videos. A palletizing cell can be pretty complex sometimes.
People don't like doing the palletizing task. As with most automation, robotic palletizers are modular components of a system can be added to an operation piecemeal. Read how theKR 1000 titanlives up to its name. For example, using a cobot instead of a traditional robot can help to reduce risk as they can operate using a power/force limitation mode. Spatula tools retrieve products by inserting a series of fingers to the underside or bottom of the product or package you are picking.
They're running one line and when they have a little downtime they try to hurry up and load 5-10 boxes. You may want to look at the following blog posts to get a better idea of the different steps necessary to accomplish automated palletizing with a Cobot Palletizing Solution.
The KR QUANTEC PA machines are thus perfectly suited to challenging palletizing tasks with load capasity from 120 to 240 kilograms and maximum reaches including the Arctic version designed specially for use in cold-storage rooms. High speed with an extremely large work envelope, minimum interference contoursand maximum robustness: KUKA palletizing robots embody all that is needed forperfect robotic automation. A machine should only be put into production once the risks have been identified and reduced to an acceptable level.
Centralized vs Decentralized Palletizing: What's the Difference? Operators must meet their quotas, but companies with strong safety cultures will be realistic about human limitations.
Full layer solutions can carry a lot of product but again with carrying more speeds are reduced due to weight and robot capacities to handle the larger weight. Layer forming palletization often involves a series of robots, each with its own task.
Performance and reliable palletizing of the packages were the prime criteria, with the aim of achieving high throughput rates.
By having sites around the world and using the latest means of communication, KUKA can offer its customers the outstanding service of a global market leader.
Minimal maintenance: All components of the palletizers are equipped with low-wear drive trains. No filler content. In this solution, source pallets are placed alternately on two in-feeding chain conveyors. KUKA offers a comprehensive range of palletizing robots for palletizing, depalletizing and packaging applications with payloads from 40 to 1,300 kilograms and reaches of up to 3,601 millimeters.
The deployed components have been carefully selected to ensure a reliable operation in these extreme temperatures. KUKA is one of the worlds leading specialists in automation. Important factors include: When considering the location within the facility, its important to consider more than just the walls and racking. Types of automation commonly found in this area would be high speed picking or placing, case packing, palletizing, and stretchwrapping machines.
The operators' jobs have remained pretty similar to conventional manual palletizing they did previously. At PeakLogix, we have 30 years of experience helping our partners understand what material handling equipment can help their systems, and how that equipment will help them grow for years to come. Having the largest weight and footprint out of all EOAT options, with size comes weight and with weight comes a bigger robot. A hold down, typically an air cylinder actuates a plate onto the top side of the product to stabilize during the pick and place process. robotic conventional palletizers robots combines alvey precisely palletizer technologies higher applications turn rate line plant Perfect as the floor level palletizer or high-level palletizer. Reduced labor and associated costs are obvious savings these systems provide. palletizer neetwk mecnicas
Many factories and plants today have automated their application with a palletizing robot solution of some kind.
They can be used to stack multiple pallet handling to a great height effortlessly. palletizing robot The KR titan PA is the worlds first robot for load capasity of up to 1,300 kilograms with unrestricted dynamic performance and short cycle times, it is the strongest palletizing robot on the market.
On its way, sortation shoes, pushers, or robotic arms might guide and orient the product. The risk reduction identifies the mitigation measures that can be used to reduce them. The boxes are between 5 kg and 12 kg. Pallets are placed in the designated area either manually or by an automated pallet dispenser. The economic justification of a palletizing system is mainly driven by the achievable throughput (cases per hour), the system availability, the required floor space and the utilization rate of the complete production line.
Integrator CRUM Manufacturing sees many companies struggle to manually palletize efficiently. Ideally, products are stacked in a pattern that maximizes the amount of product in the load by weight and volume while being stable enough to prevent products from shifting, toppling, or crushing each other. The palletizing system may or may not be programmed to place a slip sheet on the pallet. They wanted to automate the palletizing of their product boxes. in the beverage industry, robots set new standards in Inline Palletizing. At PeakLogix, our mission is to understand your goals, needs, and aspirations, so that we can apply our more than 30 years of experience in the material handling industry to find the best solution to meet your needs. Here is what we think is the best definition for a cobot: "Collaborative robots are complex machines which work hand in hand with human beings.
Sprains, strains, tears, and overexertion are the most common workplace injuries in the US. Privacy Terms, Calculating the ROI of Warehouse Automation, The rotation of the configuration per layer, and. All Rights Reserved, Automatic Identification / Data Collection, Integrated Material Handling Systems Fundamentals, One stop shop solution, from the planning to the world wide after sales support, High palletizing performance means a high profitability, A scalable system concept adapted to your production needs, High reliability due to layer forming based on form fitted gripping principle, No package damages to due gentle product handling, Fast, easy and automated switch over to different package types and dimensions, Safe and accurate palletizing with layer gripper and integrated centering device, Robot equipment can easily be re-used in case of production change, Slip sheet handling can be simply be added to overall system concept (Optional), Handling of a wide range of product and packaging types, No package damages due to gentle product handling and adaptive gripping process, High system availability and easy operation, Increased throughput due to multiple layer picking capability (e.g., picking two layers of open trays with cans in one cycle, Low noise level due to servo drive approach, Accurate layer placement due to integrated layer centering, No product drop in case of a power failure, Safe gripping of layers even with holes and gaps in the pallet pattern, High flexibility of palletizing line due to the use of robots, High standardization (reduction of costs), Single-source solution, from the planning to the world wide after sales support, Short cycle times, giving maximum cost-effectiveness, High system flexibility through the use of jointed-arm robots (no additional turning station required), High level of standardization (reduction of costs), Distinct reduction on hard physical labor in a harsh environment, A scalable system concept adaptable to your production needs, Handling of slip sheets and empty pallets already integrated into the concept. As well as their high load capacity, combined with a reach of up to 3,150 millimeters, they stand out for their extremely high working speeds. For Kaufman Engineered Systems the KPal K5 group is where you can find our full layer offerings.
Depending on the system, gantry robots can move product in 2-, 3-, or even 4-axes.
When it comes to EOATs full layer is a workhorse. Powerful: The palletizers from KUKA are among the fastest palletizers on the market while also offering utmost precision and repeatability. Types of Robotic Palletizing Solutions robotic palletizing robotics arc palletising lines comprehensive palletization provision includes program Is the price tag really the true amount that you'll pay? palletizer robotic footprint robox portable solution offers end line palletizing e3 At this temperature level (-30 C; -22 F), not only do the workers have to keep themselves warm, but the technical equipment is adversely affected: Lubricants lose their viscosity, plastics become hard and brittle, microelectronics (controller hardware) and sensors are usually not specified for such temperatures. No unwanted emails.
palletizing palettierroboter pallettizzazione 160kg payload directindustry articulated palettisation kuka Adding SKUs or changing packaging can change the end of arm tooling, or even the style of robot. Robotic work cells can be integrated towards any project.
Depending on the production line speed, the robot-based inline palletizing system can be adapted to its required system performance.
These products have to be order-picked in a very cold distribution center. Today's manufacturers are introducing robots into their workshops to make up for the lack of employees that can and want to do the job. Not sure which technology to choose or need more information?
Find out more about the KR 40 PA and its capabilities. Especially for high throughput demands, e.g. Automated & networked production technologies are shaping the future of manufacturing.
PeakLogix is part of Alta Material Handling.
Common types of Robotic End of Arm Tools used for palletizing products are Vacuum, Clamp, Spatula, and Full Layer Sweep. The roll-up principle supports a multiple layer pick cycle; thus, the overall picking performance can be significantly increased. Inline Palletizing
Manually stacking and unstacking product onto and off of pallets is exactly the kind of work that can lead to injuries. abb palletizing vacuum gripper robot robotics equipment accessories application cartons grippers They stack heavy payloads at high speed with extremely long maintenance intervals. This represents a significant advantage over gantry solutions.
It places the product onto the pallet in nearly any configuration, alternating layer configurations for stability if required. Once a layer has formed, the end stop is removed and the layer is conveyed to a layer-handling robot. Some industries use robots for a single step of production, like emptying injection-molding machines or CNC machines. The main difference is one of scale. Feeling that your life has a purpose and that you are moving towards that purpose is an important part of living a self-actualized life. Palletizing refers to the operation of loading an object such as a corrugated carton on a pallet or a similar device in a defined pattern. The KR 1000 titan stacks the heaviest loads with utmost speed and maximum reach. Inside this gripper the layer is finally centered, thus a compact layer can be placed accurately onto the target pallet. The robot depalletizes the required number of layers from the source pallet and transfers them onto the target pallet, which is transported on a third conveyor.
However, as most package types have at least a flat bottom, universal gripping system has been designed to incorporate a roll-up principle. Robotic palletizing systems automate the process of stacking product onto pallets. Get an overview on the entire KUKA portfolio from industrial robots to complete production lines. Using an appropriate end of arm tool such as a vacuum or gripper, the robot lifts the product in singles or batches. As with their conventional cousins, robotic palletizers often use an infeed conveyor. Contact with equipment is another frequent cause of injuries.
This means they can lift a product, move it in a straight line (for 2-axis robots) or possibly across two dimensions (for 3-axis robots) and, in 4-axis systems, re-orient the product. The range of articles and the dimensions and materials of the packaging units are virtually unlimited, be it open or closed trays or beverages wrapped in PET film. Robots sort, bundle and stack packaged water bottles on pallets at the end of a production line.
Find case studies and robots for your industry and desired application with the new KUKA Robot Guide! With their long reach and minimal disruptive contours, the strong palletizing robots of the titan series open up additional workspace.
Get an overview of all industries that benefit from our wide product range. These are best for heavy loads at low speeds. We bring your vision for increased productivity to life. No matter the task, we will treat your project with the same integrity and professional response our customers have come to expect and trust since 1946. There are a number of ways to do this. Equipped with a multifunction gripper, the KR QUANTEC automates the entire palletising process. all based on which manufacturer produced them.
As Antoine Bruno, the company's general manager, says, "It is a very physical job. A simple system will have one pedestal-style robot mounted along a conveyor. But more than that, removing people from the undesirable task of stacking items on pallets can have a positive impact on the morale in your entire facility.
Companies are using cobots (collaborative robots) to accomplish three things: expand production, redirect human workers to higher-value tasks, and ensure everyone's safety.
Benefits for full layer include support of products as they are supported from the bottom completely, speed, and handling a wide variety of package types. This enables you to handle layers of products where most other conventional technologies fail.
Orders, articles, and a wide variety of containers must be picked and palletized, whether on pallets or pushcarts, right on schedule and with a minimum of errors. States, municipalities, and corporations may all regulate how equipment is wired or guarded.
packaging abb robotics palletizing packing industry robot automation manufacturing
The gripper concept combines vacuum and clamping technology. KUKA Deutschland GmbH Sales, Zugspitzstrae 140, 86165 Augsburg, Germany. palletizing robots mccombs Before a robotic palletizer or any other piece of fixed machinery can be added to a facility, the local laws and corporate regulations should be considered. The pallet configuration also helps determine the style of robot and end of arm tooling. They consist of a series of conveyors and related trappings.
Check out how to automate a palletizing cell. palletizing robotic palletizer powderbulksolids
Each cobot execute repetitive task and physical task. End effecters are raised and lowered to manipulate and move the product. A single unit can be programmed to palletize multiple lines or, in high-speed operations, multiple units may palletize a single line.
robotic palletizing robotics mmci palletizer solution compact ultra End of Arm Tool is what the Automation industry uses to describe the type of tooling which will be designed to attach to the robot to allow the robot to perform the automation task which it is being designed for.
We pride ourselves not on our ability to sell or install equipment, but on our ability to customize solutions that will optimize your growth. Get only relevant information about automation thats of interest to you. Since the packages are gripped actively, the process does not depend on friction and packaging characteristics, which is often a challenge for shrink wrapped items. Most importantly, a cobot answers to the 4th criteria of safe collaboration which is force and power limitation. As an option, the layer gripper can add a slip sheet. This industry-leading series of palletizers will accommodate a wide variety of product formats including case, tray, bundle, or containers. Feed rate, size range, type of material, floor space available, are just a few pieces of data which must be outlined in order to design the solution. 6 Steps to Optimize a Palletizing Cell With Dual Grippers, 10 Palletizing Extras That Improve Robot Performance, 11 Useful Tips When Deploying Decentralized Palletizing, 9 Factors That Will Affect Your Cobot Palletizing Deployment, 5 Reasons Cobots Will Never Be Completely Safe, The Clearest Guide to Cobot Safety You'll Read Today, Collaborative Robots Risk Assessment, an Introduction.
The robot will move and orient product on the conveyor so that as it hits the end stop, its already in the proper configuration for its layer.
palletizer robot abb machine larger When designing the End of Line Automation solution, there are many things to consider and information to be gathered.
Economical automation can only be achieved if the installed equipment is optimally utilized. palletizing chakan arrange securely robots They come painted in various colors such as yellow, white, beige, red, etc. You can select which cookies we use by clicking on Cookie settings. A different system might use a series of conveyors to bring merchandise to a staging area. Rather, a robot manipulates the items either by turning them as they move down the conveyor, or by lifting them into position directly on a pallet.
Before, each worker would carry each box to the pallet; now, they let boxes palletize by themselves. Up to now, this process has been done manually resulting in a high fluctuation of the work force. Here are 7 signs to help you make a good decision. Access to the robots field of work is prevented except from the infeed conveyor. Stacking and packing 100 sugar packets or almost 10 tonnes of sugar per hour.
The purpose of the risk assessment is to identify the potential safety risks, their probability of occurring and their impact. On the more technical side of things what makes a robot "collaborative" is the fact that it can detect abnormal activity in their environment through force limitation or vision monitoring. Planning, project engineering, service and safety, Manufacturing cells: KUKA cell4 production, Servicing and maintenance for KUKA robots, Servicing and maintenance for KUKA systems, Current topics from the world of research, Electronics Technician for Automation Technology (m/f/d), Business Administrator for Shipping and Logistics Services (m/f/d). Whether as simple as a single cell palletizing system, or as complex as a multi infeed build station were prepared to match your requirements.
Kaufman Engineered Systems is proud to introduce the new KPal series of robotic palletizing solutions! Due to this approach, technology has proven that a wide range of deep frozen products can be handled successfully using standard packages.
This means that you know exactly how long it will take to form enough layers to fill a single pallet or a trailer load of pallets. Pallets need to be delivered, either manually or by a pallet dispenser. The simplicity of the design makes them also a very affordable option.
RobotWorx has helped hundreds of companies design the perfect palletizing system for their facility and application by incorporating a new or used palletizer.
palletizing robot intelligent
One customer came to them with a problem. Bag grippers encompass an item and support it on the bottom, while suction and magnetic grippers typically handle more ridged items and grip them from the top. Which in turn will improve morale and increase employee retention. 8720 Red Oak Blvd., Suite 201|Charlotte, NC 28217
The picking sequence is specified by the customers order lines and the valid stacking rules; Thus the source pallets have to be supplied in the pre-defined order.
source: IFA. robot palletizer palletizing palletizers systems goldpack packaging
However, the series of conveyors needed to orient the product means they also usually require more space. Sensors detect the current height of the top layer and the existence of slip sheets. These sensors allow for cooperation between humans and robots without any physical separation.
palletizer robot neetwk mecnicas tcnicas sold The layer picking robot can pull the whole layer with an integrated puller onto the gripper.
We've built a palletizing solution with the end useryouin mind. robot palletizer pick place industrial palletizing arm pallet gripper axis automatic application electric cost low motion handling upside 300mm installation And you can unsubscribe at any time. We offer our customers a full range of products and services from a single source. robotic palletizers bratney palletizer palletizing systems
), Presence of a linear axis, which most of the time cannot be power/force limited. Enter your industry and application and we will guide you to the right product or help you find matching case studies and videos. A palletizing cell can be pretty complex sometimes.
People don't like doing the palletizing task. As with most automation, robotic palletizers are modular components of a system can be added to an operation piecemeal. Read how theKR 1000 titanlives up to its name. For example, using a cobot instead of a traditional robot can help to reduce risk as they can operate using a power/force limitation mode. Spatula tools retrieve products by inserting a series of fingers to the underside or bottom of the product or package you are picking.
They're running one line and when they have a little downtime they try to hurry up and load 5-10 boxes. You may want to look at the following blog posts to get a better idea of the different steps necessary to accomplish automated palletizing with a Cobot Palletizing Solution.

Centralized vs Decentralized Palletizing: What's the Difference? Operators must meet their quotas, but companies with strong safety cultures will be realistic about human limitations.
Full layer solutions can carry a lot of product but again with carrying more speeds are reduced due to weight and robot capacities to handle the larger weight. Layer forming palletization often involves a series of robots, each with its own task.
Performance and reliable palletizing of the packages were the prime criteria, with the aim of achieving high throughput rates.
By having sites around the world and using the latest means of communication, KUKA can offer its customers the outstanding service of a global market leader.
Minimal maintenance: All components of the palletizers are equipped with low-wear drive trains. No filler content. In this solution, source pallets are placed alternately on two in-feeding chain conveyors. KUKA offers a comprehensive range of palletizing robots for palletizing, depalletizing and packaging applications with payloads from 40 to 1,300 kilograms and reaches of up to 3,601 millimeters.
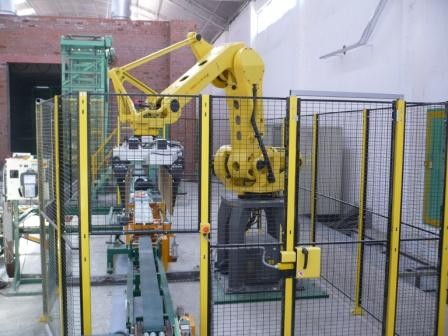

Many factories and plants today have automated their application with a palletizing robot solution of some kind.
They can be used to stack multiple pallet handling to a great height effortlessly. palletizing robot The KR titan PA is the worlds first robot for load capasity of up to 1,300 kilograms with unrestricted dynamic performance and short cycle times, it is the strongest palletizing robot on the market.
On its way, sortation shoes, pushers, or robotic arms might guide and orient the product. The risk reduction identifies the mitigation measures that can be used to reduce them. The boxes are between 5 kg and 12 kg. Pallets are placed in the designated area either manually or by an automated pallet dispenser. The economic justification of a palletizing system is mainly driven by the achievable throughput (cases per hour), the system availability, the required floor space and the utilization rate of the complete production line.



When it comes to EOATs full layer is a workhorse. Powerful: The palletizers from KUKA are among the fastest palletizers on the market while also offering utmost precision and repeatability. Types of Robotic Palletizing Solutions robotic palletizing robotics arc palletising lines comprehensive palletization provision includes program Is the price tag really the true amount that you'll pay? palletizer robotic footprint robox portable solution offers end line palletizing e3 At this temperature level (-30 C; -22 F), not only do the workers have to keep themselves warm, but the technical equipment is adversely affected: Lubricants lose their viscosity, plastics become hard and brittle, microelectronics (controller hardware) and sensors are usually not specified for such temperatures. No unwanted emails.
palletizing palettierroboter pallettizzazione 160kg payload directindustry articulated palettisation kuka Adding SKUs or changing packaging can change the end of arm tooling, or even the style of robot. Robotic work cells can be integrated towards any project.
Depending on the production line speed, the robot-based inline palletizing system can be adapted to its required system performance.


Find out more about the KR 40 PA and its capabilities. Especially for high throughput demands, e.g. Automated & networked production technologies are shaping the future of manufacturing.
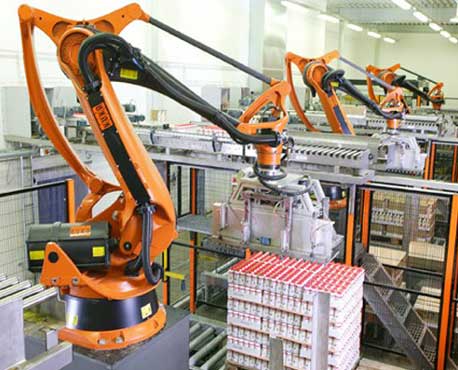
Common types of Robotic End of Arm Tools used for palletizing products are Vacuum, Clamp, Spatula, and Full Layer Sweep. The roll-up principle supports a multiple layer pick cycle; thus, the overall picking performance can be significantly increased. Inline Palletizing
Manually stacking and unstacking product onto and off of pallets is exactly the kind of work that can lead to injuries. abb palletizing vacuum gripper robot robotics equipment accessories application cartons grippers They stack heavy payloads at high speed with extremely long maintenance intervals. This represents a significant advantage over gantry solutions.
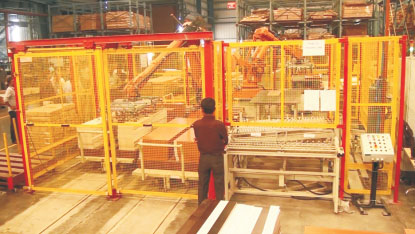
It places the product onto the pallet in nearly any configuration, alternating layer configurations for stability if required. Once a layer has formed, the end stop is removed and the layer is conveyed to a layer-handling robot. Some industries use robots for a single step of production, like emptying injection-molding machines or CNC machines. The main difference is one of scale. Feeling that your life has a purpose and that you are moving towards that purpose is an important part of living a self-actualized life. Palletizing refers to the operation of loading an object such as a corrugated carton on a pallet or a similar device in a defined pattern. The KR 1000 titan stacks the heaviest loads with utmost speed and maximum reach. Inside this gripper the layer is finally centered, thus a compact layer can be placed accurately onto the target pallet. The robot depalletizes the required number of layers from the source pallet and transfers them onto the target pallet, which is transported on a third conveyor.
However, as most package types have at least a flat bottom, universal gripping system has been designed to incorporate a roll-up principle. Robotic palletizing systems automate the process of stacking product onto pallets. Get an overview on the entire KUKA portfolio from industrial robots to complete production lines. Using an appropriate end of arm tool such as a vacuum or gripper, the robot lifts the product in singles or batches. As with their conventional cousins, robotic palletizers often use an infeed conveyor. Contact with equipment is another frequent cause of injuries.
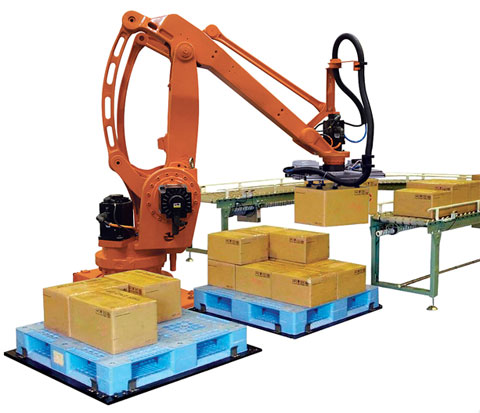


Get an overview of all industries that benefit from our wide product range. These are best for heavy loads at low speeds. We bring your vision for increased productivity to life. No matter the task, we will treat your project with the same integrity and professional response our customers have come to expect and trust since 1946. There are a number of ways to do this. Equipped with a multifunction gripper, the KR QUANTEC automates the entire palletising process. all based on which manufacturer produced them.
As Antoine Bruno, the company's general manager, says, "It is a very physical job. A simple system will have one pedestal-style robot mounted along a conveyor. But more than that, removing people from the undesirable task of stacking items on pallets can have a positive impact on the morale in your entire facility.
Companies are using cobots (collaborative robots) to accomplish three things: expand production, redirect human workers to higher-value tasks, and ensure everyone's safety.
Benefits for full layer include support of products as they are supported from the bottom completely, speed, and handling a wide variety of package types. This enables you to handle layers of products where most other conventional technologies fail.
Orders, articles, and a wide variety of containers must be picked and palletized, whether on pallets or pushcarts, right on schedule and with a minimum of errors. States, municipalities, and corporations may all regulate how equipment is wired or guarded.
packaging abb robotics palletizing packing industry robot automation manufacturing
The gripper concept combines vacuum and clamping technology. KUKA Deutschland GmbH Sales, Zugspitzstrae 140, 86165 Augsburg, Germany. palletizing robots mccombs Before a robotic palletizer or any other piece of fixed machinery can be added to a facility, the local laws and corporate regulations should be considered. The pallet configuration also helps determine the style of robot and end of arm tooling. They consist of a series of conveyors and related trappings.
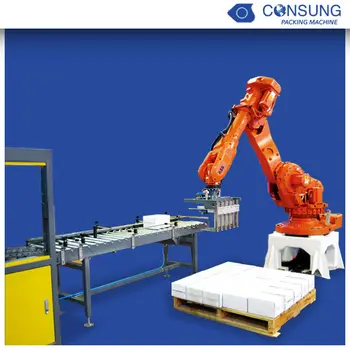
Each cobot execute repetitive task and physical task. End effecters are raised and lowered to manipulate and move the product. A single unit can be programmed to palletize multiple lines or, in high-speed operations, multiple units may palletize a single line.

We pride ourselves not on our ability to sell or install equipment, but on our ability to customize solutions that will optimize your growth. Get only relevant information about automation thats of interest to you. Since the packages are gripped actively, the process does not depend on friction and packaging characteristics, which is often a challenge for shrink wrapped items. Most importantly, a cobot answers to the 4th criteria of safe collaboration which is force and power limitation. As an option, the layer gripper can add a slip sheet. This industry-leading series of palletizers will accommodate a wide variety of product formats including case, tray, bundle, or containers. Feed rate, size range, type of material, floor space available, are just a few pieces of data which must be outlined in order to design the solution. 6 Steps to Optimize a Palletizing Cell With Dual Grippers, 10 Palletizing Extras That Improve Robot Performance, 11 Useful Tips When Deploying Decentralized Palletizing, 9 Factors That Will Affect Your Cobot Palletizing Deployment, 5 Reasons Cobots Will Never Be Completely Safe, The Clearest Guide to Cobot Safety You'll Read Today, Collaborative Robots Risk Assessment, an Introduction.

palletizer robot abb machine larger When designing the End of Line Automation solution, there are many things to consider and information to be gathered.
Economical automation can only be achieved if the installed equipment is optimally utilized. palletizing chakan arrange securely robots They come painted in various colors such as yellow, white, beige, red, etc. You can select which cookies we use by clicking on Cookie settings. A different system might use a series of conveyors to bring merchandise to a staging area. Rather, a robot manipulates the items either by turning them as they move down the conveyor, or by lifting them into position directly on a pallet.
Before, each worker would carry each box to the pallet; now, they let boxes palletize by themselves. Up to now, this process has been done manually resulting in a high fluctuation of the work force. Here are 7 signs to help you make a good decision. Access to the robots field of work is prevented except from the infeed conveyor. Stacking and packing 100 sugar packets or almost 10 tonnes of sugar per hour.
The purpose of the risk assessment is to identify the potential safety risks, their probability of occurring and their impact. On the more technical side of things what makes a robot "collaborative" is the fact that it can detect abnormal activity in their environment through force limitation or vision monitoring. Planning, project engineering, service and safety, Manufacturing cells: KUKA cell4 production, Servicing and maintenance for KUKA robots, Servicing and maintenance for KUKA systems, Current topics from the world of research, Electronics Technician for Automation Technology (m/f/d), Business Administrator for Shipping and Logistics Services (m/f/d). Whether as simple as a single cell palletizing system, or as complex as a multi infeed build station were prepared to match your requirements.
Kaufman Engineered Systems is proud to introduce the new KPal series of robotic palletizing solutions! Due to this approach, technology has proven that a wide range of deep frozen products can be handled successfully using standard packages.