Aside from that if it were me, Id get up the old tiles, level the floor (either self leveler or wood sleepers), then foam, then sub-floor. You could rebuild the stairs (OUCH!) i plan to spray foam the joist cavities against the rim joist. Your clarification would be helpful. But frankly I doubt it makes much difference. Again..no right answer here. Ive never seen someone so dedicated to answering all questions or comments.). Before that just some quick info on my basement. There are some commercially available ones that can do thicker but they are usually installed by specialty contractors. What doesnt make sense to me is that Id have to make holes through the advantech and the POLY to secure it to the floor, thus created gaps in the poly. I understand you have to have load bearing headers above the doors but is the rest of the framing normal? A self leveling floor compound might work really well. It really comes down to a personal preference and there are many different variations of the same theme. Seems to have 25psi rating I think I found the way to go unless youve seen anything negative on the Pactiv(?). I think your approach is fine. Do you have any recommendations for air quality monitoring? Where necessary, measure and cut panels to fit using a circular saw. shed insulate insulating vidalondon carpet floor The larger of the two levels (500 sq ft) is relatively levelled so Ill use a dimpled sub-floor called DMX (similar to Delta-FL), covered by OSB, then my finished floor. Kelly Bacon is a licensed general contractor with over 40 years of experience in construction, home building and remodeling, and commercial building. are and a spray foam would be utilized to fill the gaps. This sub-floor setup will be taller than the base plate of that framing. Quick question: I have about 1/2 to 3/4 inches max of space to put in a floor due to the ceiling height requirements in my basement. I can now discuss this with my friend who is also a builder himself with confident. After filling the rim joist with 2 XPS and sealing seams can I fill the rest of the cavity with unfaced insulation? Quick question when it is mentioned to seal the seams on the xps panels, is this simply the Tyvek tape on the xps seams or do you recommend caulking in between the sheets of foamboard prior to taping? Is there anything else we should be doing or should know? This poses a problem with the foam however, as each layer would be a different thickness and that might be fairly impractical. Mike You are correct, place the wall on top of the sub-floor. Either will work. The breaker box is mounted on the wall in the proposed finished area, how do I best insulated around/behind without removing the box or creating moisture issues behind? We recommend using 3/4 thick pressure treated decking. If so thats really bad! Do you mean how do you transition the floor? My pleasure. i would like to put carpet or wood laminate flooring inthe room, but i know i will need to have access to the clean out. Condensation.
(Vapor barrier towards the warm side???) Mike If you use DRI Core Id insulate the walls first then install the DRIcore. DRI-Core is a great product and weve used it before. Thanks for the great advice, its working! You can if you like, not super critical in my opinion. You recommend glueing the foam board to the concrete. If we use 1/2 foam for low ceilings, we place 6 mil vapor barrier first, then foam, then subfloor, do we still need to glue the foam to the vapor barrier, or everything will be held down when we attach the subfloor to the concrete? You can screw the sub-floor through the foam and into the concrete. Now I continually have spring water 4 under my slab. we are now on to the floor and have applied the one inch xps.but now from reading some of the above posts it seems we should have installed 6 mil poly before the foam. However, youll have a very warm comfortable floor and a whole lot less moisture in your basement. A concrete floor isnt perfectly flat, the foam wont sit perfect, so the 5/8 to 3/4 sheathing helps even it all out, and create a surface thats stiff enough for the flooring. Couple questions for you as im thinking of laying carpet in my basement (theres existing tile) but want an insulated floor: 1) I assume you recommend removing the tile first? 1. If so that is old data and I frankly dont agree with it. Todd, thanks for the great website and information. I only have a problem in the summer when the warn moist air off the lake comes in contact with the cold cement. Im alittle worried that over time the foam under the stud walls will slowly collapse. A few questions i have 1. I would let that slab cure as long as you can before installing the floor. Your method will work fine. Demetri. Most of my neighbors also had water for the first time ever. I would then install laminate on top of the Advantech. Is there a rule for how deep into the concrete the screw/nail should go?
It seems to be very strong and is only 7/8 thick. If so this is an offer you can't afford to miss! The room slopes about 2 inches from all side to the centre. Certainly doesnt hurt. Tape the seams of the foam panels with heavy-duty construction tape. The first questions is how many electrical, plumbing and heating interferences are there? I hope youll consider signing up for our FREE Weekly Newsletter, its full of tips, advice, product reviews and much more. There are no columns at all. can it just be glued down or a I am overthinking all the screws into cement is a worry ? However, my father in law is questioning whether the foam board on the floor can withstand the weight of the walls and OSB on top of it without getting crushed or being unstable. putting water pressure tank in barn room, should I lay 6ml poly on concrete then foamboard then sleepers or put the foamboard down first then poly then sleepers? Can I use OSB or do I need actual plywood over the Dricore to support the pergo floor AND can I use 1/2 inch as opposed to 3/4? I would have zero concern about the fasteners taking heat. You seem to speak my type of language.might you be an engineer? What is your opinion of one of these methods over the other 1) Dricore, 1/8 vinyl (1 overall) VS 2) poly, either 1/2 or 3/4 XPS, 5/8 Advantech, 1/8 vinyl (11/4 1-1/2 overall). You do not need, and we do not recommend, anything other than our tile to be laid on the concrete.. I figure the Delta-FL will allow for small water mishaps to drain underneath towards the sump pump hole, and the fiberrock would survive a major mishap (3-4 of water). This website uses cookies to improve your experience.
heres my odd question: i live near seattle and our 1979 home doesnt have quite the seismic restraint i would like to see, especially since we have cripple walls on 3/4 of the basement walls. 2) I have a pool table (est 1000 lbs, 26psi load through the legs) that I want on top of the subfloor. I have a basement floor that slopes towards a drain in the middle. Todd, One more question!! Have you heard of this? this would solve the water and the heat issue, will it? For starters you can go to DOW or Owens Corning and download details/specs on how to insulate a slab. Unfortunately I havent found an answer to my problem. Since it is a T&G, this means that screws need to put pn the edges or you need to put tapcons all around each board. 2. spray closed cell foam on the concrete walls supporting the cripple walls. In a perfect world Id jack up both sides of the floor joists and install a new flush beam with joist hangers. Would shimming betwee the sleepers and the subfloor be an option, or might this create uneven load distribution on the XPS? I will have to get creative with the ceiling. The concrete floor is cracked to an 1/8 inch gap along the expansion joints and is also bulged up along the expansion joints in both directions where joints meet. Will those supports need to be pressure treated as they will sit on the foundation wall? 2. Are there any issues that can arise from this? We used to do them horizontally but hey have a tendency to fall before the adhesive dries. 4. My floor is about 6 ft below grade, which is also below the frostline. Vs trying to get the plywood to lay flat by Tapconing it. Plan: sikaflex for cracks, poly, xps, cement backer board, tile. If its really a concern you could use high compression XPS which would compress even less. Also having second thoughts on the sub-flooring. Hi Todd. Will that be an issue? Should be more than enough to handle Iowas winters. The foam has more insulation value but not as easy to install, the Delta/Platon are easy to install, less insulation value. Theres no structural reason to use them. I have a bathroom i am putting in my garage and used 212 treated joist. Im more familiar with the Sikaflex, its a good product. Its only really noticable near the old sump pit where there is a more exaggerated slope. some of the walls of the concrete are exposed, but its only maybe 10-20% of the buried surface area. I have found your remarks to very informative in what seems to be a very controversial issue. Space the panels 1/4 inch apart, with a 1/2-inch gap around the perimeter. The insulation is in direct contact with the concrete. I suppose that would work out pretty well aside from the price. Just read the whole thread and I apologize if this was question was previously addressed. A self-taught carpenter, cabinetmaker, electrician,and plumber, he has renovated two 19th-century farmhouses in upstate New York and a mid-20th-century house in Austin, Texas. Im not sure its absolutely necessary to remove it. Thank you. My gut feeling would be to use 2-1/2 long fasteners which would provide 1 of penetration. First off your site is great and very helpful. Can I just lay down the XPS up to these walls? I was going to tape the XPS joints to keep the moisture from the concrete from reaching the Advantatech. 1. The only reason I am considering 3/4 is because nobody seems to stock 1 in T&G anywhere near me and they wont special order it because they have to buy it in pallets of 48. As the house is very old I needed to replace all of the beams and posts, and I just finished doing this. My plan after I get this done is to use XPS foam board and seal up like you explain on your website. My problem is I know if I submit plans to the permit office they will want some sort of documentation (IE: Manufacturers installation instructions) that document that this is an approved method to insulate a concrete slab (from above). The projects have turned out great. The sell a dimpled membrane product specifically for carpet installs. Greg At least here in this part of the Country most inspectors are used to the detail. @ Jeffrey This method could still work if you can manage to cut good tapered sleepers (this might be really hard to do). How much floor insulation do we need in New England to make the floor reasonably comfortable in the winter (average floor temp now is 50)?
Thanks for the nice compliment. Is one easier to install? Mike My pleasure. :) Im a licensed structural engineer as well and I really dont see an issue with it. I guess Id put down some poly, then the Tuff-R. 3. Again you could try ramping it. I plan on using 1 1/2 rigid foam panels on the walls before framing, but still am up in the air as to how to insulate the cellar floor. I forgot to mention earlier that your site has been a great resource in my building project.
(Vapor barrier towards the warm side???) Mike If you use DRI Core Id insulate the walls first then install the DRIcore. DRI-Core is a great product and weve used it before. Thanks for the great advice, its working! You can if you like, not super critical in my opinion. You recommend glueing the foam board to the concrete. If we use 1/2 foam for low ceilings, we place 6 mil vapor barrier first, then foam, then subfloor, do we still need to glue the foam to the vapor barrier, or everything will be held down when we attach the subfloor to the concrete? You can screw the sub-floor through the foam and into the concrete. Now I continually have spring water 4 under my slab. we are now on to the floor and have applied the one inch xps.but now from reading some of the above posts it seems we should have installed 6 mil poly before the foam. However, youll have a very warm comfortable floor and a whole lot less moisture in your basement. A concrete floor isnt perfectly flat, the foam wont sit perfect, so the 5/8 to 3/4 sheathing helps even it all out, and create a surface thats stiff enough for the flooring. Couple questions for you as im thinking of laying carpet in my basement (theres existing tile) but want an insulated floor: 1) I assume you recommend removing the tile first? 1. If so that is old data and I frankly dont agree with it. Todd, thanks for the great website and information. I only have a problem in the summer when the warn moist air off the lake comes in contact with the cold cement. Im alittle worried that over time the foam under the stud walls will slowly collapse. A few questions i have 1. I would let that slab cure as long as you can before installing the floor. Your method will work fine. Demetri. Most of my neighbors also had water for the first time ever. I would then install laminate on top of the Advantech. Is there a rule for how deep into the concrete the screw/nail should go?
It seems to be very strong and is only 7/8 thick. If so this is an offer you can't afford to miss! The room slopes about 2 inches from all side to the centre. Certainly doesnt hurt. Tape the seams of the foam panels with heavy-duty construction tape. The first questions is how many electrical, plumbing and heating interferences are there? I hope youll consider signing up for our FREE Weekly Newsletter, its full of tips, advice, product reviews and much more. There are no columns at all. can it just be glued down or a I am overthinking all the screws into cement is a worry ? However, my father in law is questioning whether the foam board on the floor can withstand the weight of the walls and OSB on top of it without getting crushed or being unstable. putting water pressure tank in barn room, should I lay 6ml poly on concrete then foamboard then sleepers or put the foamboard down first then poly then sleepers? Can I use OSB or do I need actual plywood over the Dricore to support the pergo floor AND can I use 1/2 inch as opposed to 3/4? I would have zero concern about the fasteners taking heat. You seem to speak my type of language.might you be an engineer? What is your opinion of one of these methods over the other 1) Dricore, 1/8 vinyl (1 overall) VS 2) poly, either 1/2 or 3/4 XPS, 5/8 Advantech, 1/8 vinyl (11/4 1-1/2 overall). You do not need, and we do not recommend, anything other than our tile to be laid on the concrete.. I figure the Delta-FL will allow for small water mishaps to drain underneath towards the sump pump hole, and the fiberrock would survive a major mishap (3-4 of water). This website uses cookies to improve your experience.
heres my odd question: i live near seattle and our 1979 home doesnt have quite the seismic restraint i would like to see, especially since we have cripple walls on 3/4 of the basement walls. 2) I have a pool table (est 1000 lbs, 26psi load through the legs) that I want on top of the subfloor. I have a basement floor that slopes towards a drain in the middle. Todd, One more question!! Have you heard of this? this would solve the water and the heat issue, will it? For starters you can go to DOW or Owens Corning and download details/specs on how to insulate a slab. Unfortunately I havent found an answer to my problem. Since it is a T&G, this means that screws need to put pn the edges or you need to put tapcons all around each board. 2. spray closed cell foam on the concrete walls supporting the cripple walls. In a perfect world Id jack up both sides of the floor joists and install a new flush beam with joist hangers. Would shimming betwee the sleepers and the subfloor be an option, or might this create uneven load distribution on the XPS? I will have to get creative with the ceiling. The concrete floor is cracked to an 1/8 inch gap along the expansion joints and is also bulged up along the expansion joints in both directions where joints meet. Will those supports need to be pressure treated as they will sit on the foundation wall? 2. Are there any issues that can arise from this? We used to do them horizontally but hey have a tendency to fall before the adhesive dries. 4. My floor is about 6 ft below grade, which is also below the frostline. Vs trying to get the plywood to lay flat by Tapconing it. Plan: sikaflex for cracks, poly, xps, cement backer board, tile. If its really a concern you could use high compression XPS which would compress even less. Also having second thoughts on the sub-flooring. Hi Todd. Will that be an issue? Should be more than enough to handle Iowas winters. The foam has more insulation value but not as easy to install, the Delta/Platon are easy to install, less insulation value. Theres no structural reason to use them. I have a bathroom i am putting in my garage and used 212 treated joist. Im more familiar with the Sikaflex, its a good product. Its only really noticable near the old sump pit where there is a more exaggerated slope. some of the walls of the concrete are exposed, but its only maybe 10-20% of the buried surface area. I have found your remarks to very informative in what seems to be a very controversial issue. Space the panels 1/4 inch apart, with a 1/2-inch gap around the perimeter. The insulation is in direct contact with the concrete. I suppose that would work out pretty well aside from the price. Just read the whole thread and I apologize if this was question was previously addressed. A self-taught carpenter, cabinetmaker, electrician,and plumber, he has renovated two 19th-century farmhouses in upstate New York and a mid-20th-century house in Austin, Texas. Im not sure its absolutely necessary to remove it. Thank you. My gut feeling would be to use 2-1/2 long fasteners which would provide 1 of penetration. First off your site is great and very helpful. Can I just lay down the XPS up to these walls? I was going to tape the XPS joints to keep the moisture from the concrete from reaching the Advantatech. 1. The only reason I am considering 3/4 is because nobody seems to stock 1 in T&G anywhere near me and they wont special order it because they have to buy it in pallets of 48. As the house is very old I needed to replace all of the beams and posts, and I just finished doing this. My plan after I get this done is to use XPS foam board and seal up like you explain on your website. My problem is I know if I submit plans to the permit office they will want some sort of documentation (IE: Manufacturers installation instructions) that document that this is an approved method to insulate a concrete slab (from above). The projects have turned out great. The sell a dimpled membrane product specifically for carpet installs. Greg At least here in this part of the Country most inspectors are used to the detail. @ Jeffrey This method could still work if you can manage to cut good tapered sleepers (this might be really hard to do). How much floor insulation do we need in New England to make the floor reasonably comfortable in the winter (average floor temp now is 50)?
Thanks for the nice compliment. Is one easier to install? Mike My pleasure. :) Im a licensed structural engineer as well and I really dont see an issue with it. I guess Id put down some poly, then the Tuff-R. 3. Again you could try ramping it. I plan on using 1 1/2 rigid foam panels on the walls before framing, but still am up in the air as to how to insulate the cellar floor. I forgot to mention earlier that your site has been a great resource in my building project.

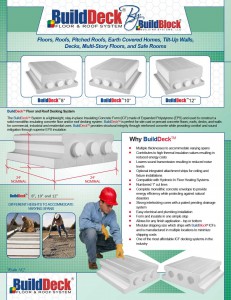
