For highly exothermic plug flow reactors such as gas reactors, coils provide more effective cooling from direct process contact in the core and high fluid velocities inside and outside the coils. Manufacturing is on the verge of a Fourth Industrial Revolution. Top Tips to Optimize Direct Steam Heating Applications, Top Tips to Optimize Tank Heating Applications, https://automation.isa.org/how-to-make-transitions-between-cooling-and-heating-smooth-and-fast/. Steam injection heating of hot water can deliver improvedtemperature control, which equates to improved product quality, increased production efficiency and reduced operation costs. Thus, being able to influence the temperature is of upmost importance for chemical industries. If the injection heater has hundreds of small orifices, the bubbles are extremely small and are rapidly and quietly mixed into the water. A recommendation for installation, including coil diameter and layout. Jackets offer a more even heat transfer distribution. At Sigma Thermal, we produce a range of thermal fluid heating systems suited for reactor heating and cooling applications. Part 4. To calculate the heat transfer area, a value for the overall heat transfer coefficient, U, must be chosen. A second valve (starting valve) to pass the difference between the capacity of the first valve, and the maximum flowrate.
limpet cstr ction Heating Vats and Tanks by Steam Injections, Steam Consumption of Pipes and Air Heaters, Previous - Energy Consumption of Tanks and Vats, Next - Heating Vats and Tanks by Steam Injections, Mean steam/water temperature difference around 30 C, Mean steam/water temperature difference around 60 C, Mean steam/water temperature difference around 110 C, (<2 bar g) with natural circulation of water, (>6 bar g) with natural circulation of water, (<2 bar g) with assisted circulation of water, (>6 bar g) with assisted circulation of water. Sodium dichromate in the amount of 1 lb/100 gal should be added. Fill out the below and one of our volume product specialists will be back toyou shortly.
Extremely happy with purchase! The heat transfer area (the vessel wall surface area), can be calculated in the same manner as with a steam coil, using Equation 2.5.3 and the overall heat transfer coefficients provided in Table 2.10.4.
* 5V/2A battery is required for use and is not included with the vest. Lightweight synthetic insulation provides lasting warmth and comfort that will help keep you in the field longer and protect you from the harshest elements. Arbitrarily selecting 32 mm pipe as a good compromise between robustness and workability: It is necessary to confirm the steam velocity through the connecting tubes: On the basis of proportionality of heat transfer area, the steam header will condense: The design and layout of the steam coil will depend on the process fluid being heated. Pass the condensate load when steam pressure in the coil equals the condensate backpressure, i.e.
Email Enquiries: [emailprotected] reactor jacket pipe half cre heating rust) which may have formed. that is used and at what flow. The first heat exchanger unit cools the brine down to 20C with another ethylene glycol brine from a chiller. However, for reasons previously explained, two valves may be better. Scentlok is the real deal! Waterlogging can, in some applications, be costly. A single control valve, large enough to cope with the maximum flowrate encountered at start-up, may be unable to control flow accurately at the minimum expected flowrate.
By no means a deal breaker at all and still very happy with purchase -, BE:1 Reactor Heated Vest Plus Reviews - page 2, Ultimate Stretch Fleece Beanie/Gaiter Combo, BE:1 Fortress Glove True Timber O2 Whitetail, Savanna Aero Attack 1/4 Zip Shirt Mossy Oak Terra Gila, loc_en_US, sid_1031209, prod, sort_[SortEntry(order=RELEVANCE, direction=DESCENDING)]. External reset feedback of the actual response of the valve or secondary flow is used to prevent the jacket or coil temperature PID output from trying to change faster than the setpoint rate limits will allow. The range of figures shown in Table 2.10.1 demonstrates the difficulty in providing definitive U values. In the case of fluids other than water, the heat transfer coefficient will vary even more widely due to the way in which viscosity varies with temperature. When the seal is ultimately broken, a smaller volume of water will return to the heating coil than with an unrestricted large bore riser, but as the water seal arrangement requires a smaller volume of condensate to form a water seal, it will immediately re-form. The direct steam injection heating method is effective for both continuous reactors and batch reactors. Asynt offer a range of jacketed reactors for chemical processes up to 100L. The outer jacket serves as vacuum insulation, ensuring that the vessel stays at the desired temperature and preventing condensation/ice formation at ultra-low temperatures. Please use caution when operating. Some coolants may decompose to acid component when exposed to heat/steam, leading to corrosion of both the vessel and jacket steel. Options include: The use of tank coils is particularly common in marine applications where cargoes of crude oil, edible oils, tallow and molasses are heated in deep tanks. This can result in a highly corrosive condition. Often both heating and cooling are often required. reactor chemical vessel stainless steel jacket heating cooling mixing tank Sign up now to receive exclusive discounts, bonus point opportunities and special offers, as well as updates on the latest products and promotions. tank heating double steam jacketed larger Heat exchangers are used for some jacket temperature control systems and for all process recirculation temperature control systems (discussed in Part 3 and Part 4 of this blog series). These recommended rates are empirically derived, and will generally ensure that a generous safety margin applies to the coil sizing. Once again Scentlok leads the way with their Innovative and highly engineered Outdoor Products! conditions: If the steam trap is only sized on the first condition, it is possible that it may not pass the stall load (the condition where the product approaches its required temperature and the control valve modulates to reduce steam pressure). See Greg McMillan's ISA book Advances in Reactor Measurement and Control for an extensive view of practical opportunities for designing control strategies to achieve product quality and maximize yield and capacity in different types of fermenters, bioreactors, and chemical reactors. In these systems, the heat is transferred across a heat transfer surface. Previously, gasketed heat exchangers were used. Heat transfer coefficient from steam/coil/liquid, U = 650 W/m C. Often, quite complex sys tems are needed for tempering the reactor. One solution would be to run a bank of parallel pipes between steam and condensate manifolds, set at different heights to encourage condensate to run Cooling and heating can be applied directly to the vessel by heat transfer surfaces in the vessel exterior (e.g., jackets) or interior (e.g., coils) or indirectly via a process recirculation stream. I was able to travel light and leave home without a heavier jacket. Many jacketed reactors can be connected to laboratory automation software, offering the user precise control over the temperature and process of the reactor, providing computerized data and reporting.
Use ScentLok Oz ozone generators to clean and refreshyour carbon clothing before your hunts, enhancing your time in the field. For use as a heat or cold shield on Chemglass jacketed reactors. Optional multi-layer stirring blades for optimal reaction results. Greg was also an affiliate professor for Washington University in Saint Louis. In extreme cases the average pressure used may be as low as 40% of the inletpressure. Table 2.10.2 Heat emission rates for steam coils submerged in miscellaneous liquids. Tank coils in large circular tanks tend to be of robust construction, and are often able to withstand such stresses. A DN40 control valve with a larger Kvs of 25 would therefore need to be selected for the application. Assisted circulation (such as stirring) that will induce forced convection, will also result in higher coefficients. chemical If one valve is to be used, this valve must ensure the maximum heat load is catered for, while maintaining the required steam pressure in the coil to assist the drainage of condensate from it at start-up. Once the heating cycle is complete, the PSX heater can be closed to allow for the cooling process to begin. Maximum heat transfer (and hence steam demand) will occur when the temperature difference between the steam and the process fluid is at its maximum, and should take into consideration the extra pipe area allowed for fouling. After the desired chemical reaction takes place, the vessel goes through a cool down phase to bring the solution back to safe handling temperatures. Steam jackets - Steam circulates in the annular space between a jacket and the vessel walls, and heat is transferred through the wall of the vessel.
Like other BE:1 Reactor Series garments, this unique, multifunction vest is engineered with Thinsulate insulation to create warmth without the bulk so it easily integrates into any layering system.
** Commercial molasses frequently contains water and the viscosity is muchlower. This blog covers numerous topics on industrial automation such as operations & management, continuous & batch processing, connectivity, manufacturing & machine control, and Industry 4.0. Use external reset using a fast read back of actual valve position and directional move suppression to help prevent oscillations. Insulating jacket is made from a heavy fiberglass fabric on the inside with a silicone-coated fiberglass fabric on the outside. This will provide a heating area of: Consequently 7 m - 1 m = 6 m of heat transfer area is still required, and must be provided by the connecting pipes. Cold air at 4 C flowing at 3 m/s can soon freeze condensate locked in the coils, resulting in premature and unwarranted failure. 1000l It quickly warms up and has 3 settings depending on your situation. Problems can however occur in rectangular tanks (which tend to be smaller), where vibration in the coil will have more of an effect on the tank structure. The second heat exchanger cools the brine to around 10C with city water. When the locked steam condenses and the steam trap opens, a slug of water is discharged up the riser.
Jacketed vessels may also be lagged, or may contain an internal air space surrounding the jacket. jacketed reactor vessel conventional jackets shell High turn down on temperature (up to 8:1) for better cascade temperature control. Visit our ISA Global Cybersecurity Alliance (ISAGCA) blog here. Each reactor features adjustable stirring speeds and a constant pressure feeding funnel that allows you to add material to the vessel at a uniform and controlled speed. The glass lining will offer an additional corrosion resistant layer. Featuring an ultra-quiet premium micro tricot fabric, three-pocket design, and proven-deadly Carbon AlloyTM technology for maximum odor adsorption, the multifunctional BE:1 Reactor Vest PLUS is available in six different sizes and three camo patterns, plus black, to meet the individual needs and preferences of any hunter. This caused the wrong brine to end up in the wrong system (cooling tower water in the steam system etc.) The coil has been sized on mean heat transfer values. Need help with an order or return? To achieve the mean coil temperature, an average steam pressure of approximately 75% of the inlet pressure may be used. The steam manifold should be 100 mm diameter as determined by the previous velocity calculation. Our industry leading technology combines activated carbon, treated carbon and zeolite concealed between fabrics. The most commonly used type of steam jacket consists simply of an outer cylinder surrounding the vessel, as shown in Figure 2.10.4. I'm ALWAYS cold. This website uses cookies. Whilst the next two headings, Sizing the control valve and The condensate removal device are included in this Module, the new reader should refer to later Blocks and Modules in The Learning Centre for full and comprehensive information, before attempting sizing and selection of equipment. Presently, Greg is a part time modeling and control consultant in Technology for Process Simulation for Emerson Automation Solutions specializing in the use of the virtual plant for exploring new opportunities. Insight: Throttling a utility makeup flow instead of the jacket or coil flow helps to keep the jacket or coil dynamics constant and reduces fouling of the utility side of heat transfer surfaces. Split ranged control is used to go back and forth between heating and cooling. Continuing with Example 2.10.1 the maximum steam load is 850 kg/h and the coil is designed to deliver this at a pressure of 1.1 bar g. A steam valve sizing chart would show that a Kv of about 20 is required to pass 850 kg/h of steam with a pressure of 2.6 bar g at the inlet of the control valve, and Critical Pressure Drop (CPD) across the valve. The selection and sizing of the condensate removal device will be very much influenced by the condensate backpressure. All glassware is hand-made from food grade high borosilicate glass that is heat/cold/corrosion-resistant. Overall, the vest works and will keep you in the stand longer, but as it is currently made, is not fire and forget. Float traps are steam traps designed to modulate and release condensate close to steam temperature, offering maximum plant performance, maximum plant life, and maximum return on plant investment. (a) Consider the maximum heating capacity of the coil Q(coil), Part 5 A recommendation for installation, including coil diameter and layout. Make sure the utility valves have minimal backlash and stiction especially near the closed position that is the split range point. In their plant at Cameri outside of Milan, Italy, they have over 35 large reactors in process, all with a need for temperature regulation. Presently, Greg is a part time modeling and control consultant in Technology for Process Simulation for Emerson Automation Solutions specializing in the use of the digital twin for exploring new opportunities. These cookies will be stored in your browser only with your consent. Single jacket systems use a chiller to circulate liquid all around the reactor whereas double jacket systems use the chiller to circulate the liquid through the inner jacket. Any cookies that may not be particularly necessary for the website to function and is used specifically to collect user personal data via analytics, ads, other embedded contents are termed as non-necessary cookies. Greg is the author of numerous books on process control, including Advances in Reactor Measurement and Control and Essentials of Modern Measurements and Final Elements in the Process Industry. Extra caution must also be taken when operating with air-reactive materials, especially under vacuum. reactor jacketed vessel heating water process chemical typical ap As the temperature controller output increases from the split range point to the 100%, the heating valve goes from closed to wide open. The stall load may be considerable. Furthermore, problems occurred because of mistakes being made when emptying and filling the jacket. oil kettle reaction conduction heating steam heat jacket equipment A short length of coil with a large diameter may not provide adequate temperature distribution. This was a very slow responding system. This will help steam to flow and push condensate through the coils.
limpet cstr ction Heating Vats and Tanks by Steam Injections, Steam Consumption of Pipes and Air Heaters, Previous - Energy Consumption of Tanks and Vats, Next - Heating Vats and Tanks by Steam Injections, Mean steam/water temperature difference around 30 C, Mean steam/water temperature difference around 60 C, Mean steam/water temperature difference around 110 C, (<2 bar g) with natural circulation of water, (>6 bar g) with natural circulation of water, (<2 bar g) with assisted circulation of water, (>6 bar g) with assisted circulation of water. Sodium dichromate in the amount of 1 lb/100 gal should be added. Fill out the below and one of our volume product specialists will be back toyou shortly.

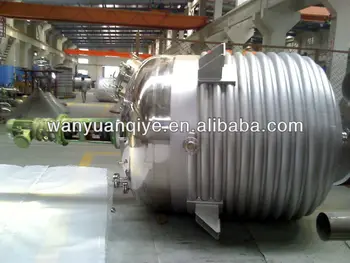
By no means a deal breaker at all and still very happy with purchase -, BE:1 Reactor Heated Vest Plus Reviews - page 2, Ultimate Stretch Fleece Beanie/Gaiter Combo, BE:1 Fortress Glove True Timber O2 Whitetail, Savanna Aero Attack 1/4 Zip Shirt Mossy Oak Terra Gila, loc_en_US, sid_1031209, prod, sort_[SortEntry(order=RELEVANCE, direction=DESCENDING)]. External reset feedback of the actual response of the valve or secondary flow is used to prevent the jacket or coil temperature PID output from trying to change faster than the setpoint rate limits will allow. The range of figures shown in Table 2.10.1 demonstrates the difficulty in providing definitive U values. In the case of fluids other than water, the heat transfer coefficient will vary even more widely due to the way in which viscosity varies with temperature. When the seal is ultimately broken, a smaller volume of water will return to the heating coil than with an unrestricted large bore riser, but as the water seal arrangement requires a smaller volume of condensate to form a water seal, it will immediately re-form. The direct steam injection heating method is effective for both continuous reactors and batch reactors. Asynt offer a range of jacketed reactors for chemical processes up to 100L. The outer jacket serves as vacuum insulation, ensuring that the vessel stays at the desired temperature and preventing condensation/ice formation at ultra-low temperatures. Please use caution when operating. Some coolants may decompose to acid component when exposed to heat/steam, leading to corrosion of both the vessel and jacket steel. Options include: The use of tank coils is particularly common in marine applications where cargoes of crude oil, edible oils, tallow and molasses are heated in deep tanks. This can result in a highly corrosive condition. Often both heating and cooling are often required. reactor chemical vessel stainless steel jacket heating cooling mixing tank Sign up now to receive exclusive discounts, bonus point opportunities and special offers, as well as updates on the latest products and promotions. tank heating double steam jacketed larger Heat exchangers are used for some jacket temperature control systems and for all process recirculation temperature control systems (discussed in Part 3 and Part 4 of this blog series). These recommended rates are empirically derived, and will generally ensure that a generous safety margin applies to the coil sizing. Once again Scentlok leads the way with their Innovative and highly engineered Outdoor Products! conditions: If the steam trap is only sized on the first condition, it is possible that it may not pass the stall load (the condition where the product approaches its required temperature and the control valve modulates to reduce steam pressure). See Greg McMillan's ISA book Advances in Reactor Measurement and Control for an extensive view of practical opportunities for designing control strategies to achieve product quality and maximize yield and capacity in different types of fermenters, bioreactors, and chemical reactors. In these systems, the heat is transferred across a heat transfer surface. Previously, gasketed heat exchangers were used. Heat transfer coefficient from steam/coil/liquid, U = 650 W/m C. Often, quite complex sys tems are needed for tempering the reactor. One solution would be to run a bank of parallel pipes between steam and condensate manifolds, set at different heights to encourage condensate to run Cooling and heating can be applied directly to the vessel by heat transfer surfaces in the vessel exterior (e.g., jackets) or interior (e.g., coils) or indirectly via a process recirculation stream. I was able to travel light and leave home without a heavier jacket. Many jacketed reactors can be connected to laboratory automation software, offering the user precise control over the temperature and process of the reactor, providing computerized data and reporting.
Use ScentLok Oz ozone generators to clean and refreshyour carbon clothing before your hunts, enhancing your time in the field. For use as a heat or cold shield on Chemglass jacketed reactors. Optional multi-layer stirring blades for optimal reaction results. Greg was also an affiliate professor for Washington University in Saint Louis. In extreme cases the average pressure used may be as low as 40% of the inletpressure. Table 2.10.2 Heat emission rates for steam coils submerged in miscellaneous liquids. Tank coils in large circular tanks tend to be of robust construction, and are often able to withstand such stresses. A DN40 control valve with a larger Kvs of 25 would therefore need to be selected for the application. Assisted circulation (such as stirring) that will induce forced convection, will also result in higher coefficients. chemical If one valve is to be used, this valve must ensure the maximum heat load is catered for, while maintaining the required steam pressure in the coil to assist the drainage of condensate from it at start-up. Once the heating cycle is complete, the PSX heater can be closed to allow for the cooling process to begin. Maximum heat transfer (and hence steam demand) will occur when the temperature difference between the steam and the process fluid is at its maximum, and should take into consideration the extra pipe area allowed for fouling. After the desired chemical reaction takes place, the vessel goes through a cool down phase to bring the solution back to safe handling temperatures. Steam jackets - Steam circulates in the annular space between a jacket and the vessel walls, and heat is transferred through the wall of the vessel.
Like other BE:1 Reactor Series garments, this unique, multifunction vest is engineered with Thinsulate insulation to create warmth without the bulk so it easily integrates into any layering system.
** Commercial molasses frequently contains water and the viscosity is muchlower. This blog covers numerous topics on industrial automation such as operations & management, continuous & batch processing, connectivity, manufacturing & machine control, and Industry 4.0. Use external reset using a fast read back of actual valve position and directional move suppression to help prevent oscillations. Insulating jacket is made from a heavy fiberglass fabric on the inside with a silicone-coated fiberglass fabric on the outside. This will provide a heating area of: Consequently 7 m - 1 m = 6 m of heat transfer area is still required, and must be provided by the connecting pipes. Cold air at 4 C flowing at 3 m/s can soon freeze condensate locked in the coils, resulting in premature and unwarranted failure. 1000l It quickly warms up and has 3 settings depending on your situation. Problems can however occur in rectangular tanks (which tend to be smaller), where vibration in the coil will have more of an effect on the tank structure. The second heat exchanger cools the brine to around 10C with city water. When the locked steam condenses and the steam trap opens, a slug of water is discharged up the riser.
Jacketed vessels may also be lagged, or may contain an internal air space surrounding the jacket. jacketed reactor vessel conventional jackets shell High turn down on temperature (up to 8:1) for better cascade temperature control. Visit our ISA Global Cybersecurity Alliance (ISAGCA) blog here. Each reactor features adjustable stirring speeds and a constant pressure feeding funnel that allows you to add material to the vessel at a uniform and controlled speed. The glass lining will offer an additional corrosion resistant layer. Featuring an ultra-quiet premium micro tricot fabric, three-pocket design, and proven-deadly Carbon AlloyTM technology for maximum odor adsorption, the multifunctional BE:1 Reactor Vest PLUS is available in six different sizes and three camo patterns, plus black, to meet the individual needs and preferences of any hunter. This caused the wrong brine to end up in the wrong system (cooling tower water in the steam system etc.) The coil has been sized on mean heat transfer values. Need help with an order or return? To achieve the mean coil temperature, an average steam pressure of approximately 75% of the inlet pressure may be used. The steam manifold should be 100 mm diameter as determined by the previous velocity calculation. Our industry leading technology combines activated carbon, treated carbon and zeolite concealed between fabrics. The most commonly used type of steam jacket consists simply of an outer cylinder surrounding the vessel, as shown in Figure 2.10.4. I'm ALWAYS cold. This website uses cookies. Whilst the next two headings, Sizing the control valve and The condensate removal device are included in this Module, the new reader should refer to later Blocks and Modules in The Learning Centre for full and comprehensive information, before attempting sizing and selection of equipment. Presently, Greg is a part time modeling and control consultant in Technology for Process Simulation for Emerson Automation Solutions specializing in the use of the virtual plant for exploring new opportunities. Insight: Throttling a utility makeup flow instead of the jacket or coil flow helps to keep the jacket or coil dynamics constant and reduces fouling of the utility side of heat transfer surfaces. Split ranged control is used to go back and forth between heating and cooling. Continuing with Example 2.10.1 the maximum steam load is 850 kg/h and the coil is designed to deliver this at a pressure of 1.1 bar g. A steam valve sizing chart would show that a Kv of about 20 is required to pass 850 kg/h of steam with a pressure of 2.6 bar g at the inlet of the control valve, and Critical Pressure Drop (CPD) across the valve. The selection and sizing of the condensate removal device will be very much influenced by the condensate backpressure. All glassware is hand-made from food grade high borosilicate glass that is heat/cold/corrosion-resistant. Overall, the vest works and will keep you in the stand longer, but as it is currently made, is not fire and forget. Float traps are steam traps designed to modulate and release condensate close to steam temperature, offering maximum plant performance, maximum plant life, and maximum return on plant investment. (a) Consider the maximum heating capacity of the coil Q(coil), Part 5 A recommendation for installation, including coil diameter and layout. Make sure the utility valves have minimal backlash and stiction especially near the closed position that is the split range point. In their plant at Cameri outside of Milan, Italy, they have over 35 large reactors in process, all with a need for temperature regulation. Presently, Greg is a part time modeling and control consultant in Technology for Process Simulation for Emerson Automation Solutions specializing in the use of the digital twin for exploring new opportunities. These cookies will be stored in your browser only with your consent. Single jacket systems use a chiller to circulate liquid all around the reactor whereas double jacket systems use the chiller to circulate the liquid through the inner jacket. Any cookies that may not be particularly necessary for the website to function and is used specifically to collect user personal data via analytics, ads, other embedded contents are termed as non-necessary cookies. Greg is the author of numerous books on process control, including Advances in Reactor Measurement and Control and Essentials of Modern Measurements and Final Elements in the Process Industry. Extra caution must also be taken when operating with air-reactive materials, especially under vacuum. reactor jacketed vessel heating water process chemical typical ap As the temperature controller output increases from the split range point to the 100%, the heating valve goes from closed to wide open. The stall load may be considerable. Furthermore, problems occurred because of mistakes being made when emptying and filling the jacket. oil kettle reaction conduction heating steam heat jacket equipment A short length of coil with a large diameter may not provide adequate temperature distribution. This was a very slow responding system. This will help steam to flow and push condensate through the coils.